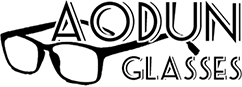
As technology continues to play a central role in daily life, many consumers are turning to blue light blocking reading glasses to reduce the strain caused by prolonged screen use. These specialized glasses offer various benefits for individuals who frequently engage with digital devices, from computers to smartphones. In addition to their health benefits, the manufacturing process of portable reading glasses has also evolved, making them more accessible and practical for a wide range of users.
The Manufacturing of Portable Reading Glasses
Portable reading glasses have become an essential item for many individuals who need vision correction for close-up tasks such as reading, working on a computer, or crafting. Their lightweight, compact design makes them easy to carry in a bag or pocket, ensuring that people can use them whenever and wherever needed. The manufacturing process behind these glasses has advanced significantly over the years, incorporating technology and innovation to improve both functionality and convenience.
1. Materials Selection
The production of portable reading glasses starts with the selection of materials. Frame materials vary widely, but some of the common materials used include plastic, metal, and acetate. Plastics like polycarbonate are lightweight and durable, making them ideal for portable glasses. Acetate frames, which are made from plant-based fibers, offer a more eco-friendly option. Metals such as stainless steel or titanium are also popular due to their strength, lightweight properties, and corrosion resistance.
The lenses themselves are usually made from high-quality optical plastics such as CR-39 or polycarbonate. These materials are chosen for their clarity, scratch resistance, and lightweight properties. For portable reading glasses, lenses are often manufactured with single vision prescriptions, though some models may feature bifocal or progressive lenses for those with more complex vision needs.
2. Precision Manufacturing of Frames and Lenses
Once materials are selected, the next step in the manufacturing process involves precision cutting of both the frames and the lenses. Frame designs are often computer-generated using 3D modeling technology, allowing for accurate dimensions and a custom fit for the wearer's needs. Once the frame design is finalized, it is cut, shaped, and assembled through a process that may involve injection molding or stamping, depending on the material used.
For the lenses, optical clarity is critical. The lenses are cut to fit the frame's specifications, with careful attention to the curvature required for vision correction. After cutting, the lenses are polished and coated to enhance durability, reduce glare, and provide additional protection against scratches. If the lenses are tinted for blue light blocking or UV protection, additional layers are applied during this stage to improve the lens's functionality.
3. Customization and Lens Coatings
Some manufacturers offer customization options for portable reading glasses. Consumers can choose from various lens coatings, including anti-reflective coatings to reduce glare, scratch-resistant coatings for improved durability, and blue light blocking filters for those who spend a lot of time in front of digital screens. These coatings are typically applied during the lens manufacturing process to ensure that the final product meets the consumer's specific needs.
4. Quality Control
Quality control is a crucial part of the portable reading glasses manufacturing process. After the frames and lenses are assembled, each pair of glasses undergoes rigorous testing to ensure they meet industry standards for optical clarity, comfort, and durability. Frames are tested for their ability to withstand everyday wear and tear, while lenses are examined for any imperfections that could affect vision.
5. Packaging and Distribution
After passing quality control, the portable reading glasses are carefully packaged for distribution. The compact, lightweight design of these glasses makes them ideal for retail shelves and online sales. Manufacturers often include protective cases to ensure that the glasses remain in good condition during transit and after purchase. Once packaged, they are distributed to various retailers and directly to consumers.